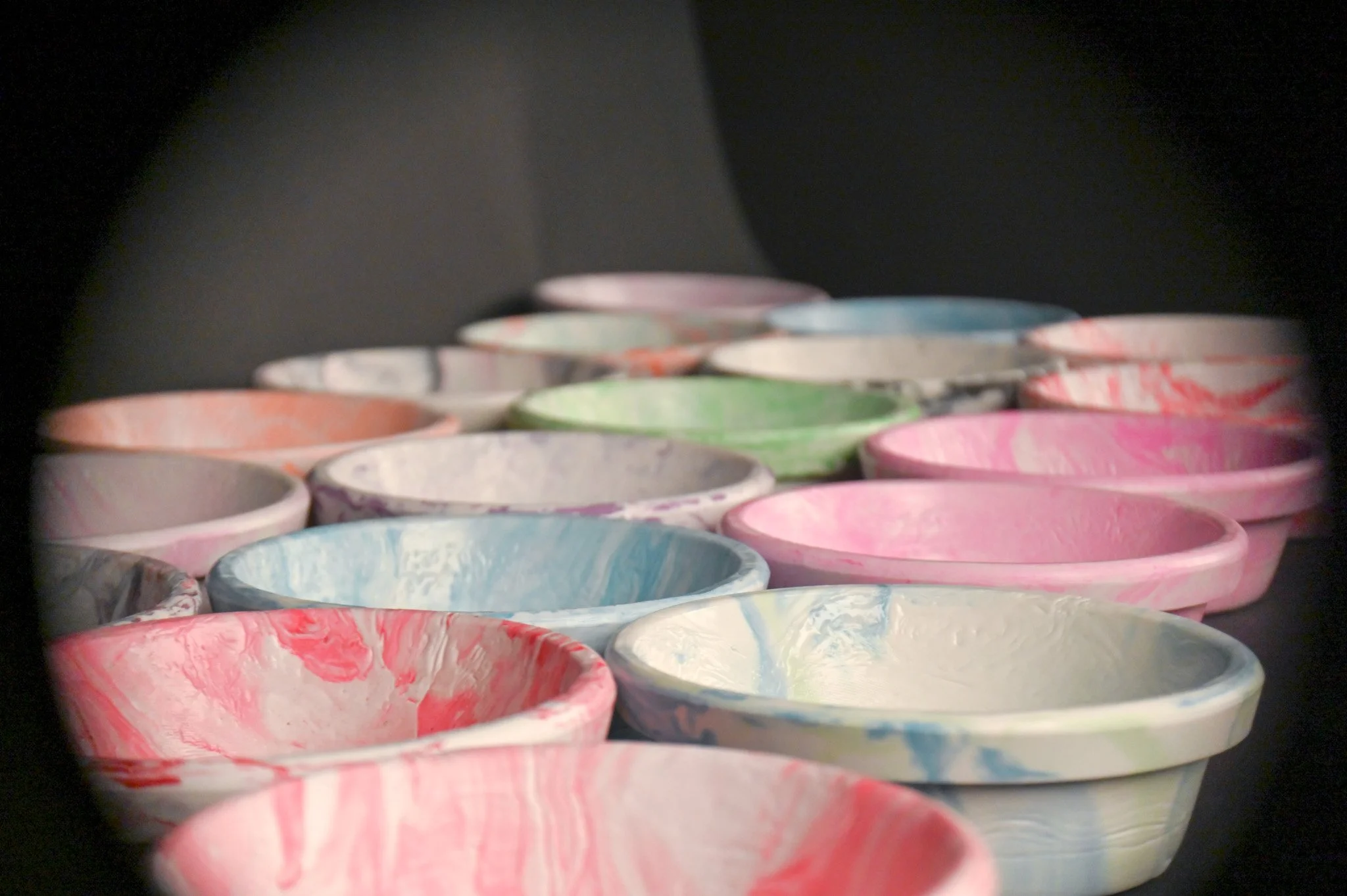
PUPCYCLED
A “rebarkable” dog bowl made from recycled plastic
This bowl is crafted from landfill-bound frisbees and repurposed industrial food containers, transforming pet toy waste into a durable, beautiful product that positively impacts the environment. PUPCYCLED was sold at EPOP 2024.
Product Photos
What is ?
EPOP is a course where students apply design theory to real-world projects.
In teams of three, students develop a product from sketch to scale, culminating in its sale at the Pearl Street Firefly market.
This experiential learning fosters a sense of entrepreneurship and inspires sustainable design practices.
My team up-cycled secondhand frisbees and food containers into unique dog bowls.
We cleaned and cut both plastics, then heated them with a panini press to soften and twist into marbled patterns.
Using a CNC-milled compression mold, we formed the bowls, then finished them with laser-engraved tags secured to the bottom with screws.
Process Video
Prototype 1: Tennis Ball Bowl
Our initial concept involved repurposing tennis balls into foldable dog bowls.
We used the ball's felt as an outer shell and synthetic fabric as the liner.
In response to feedback, we redesigned the prototype with a used firehose shell for added structure and durability.
However, designing a durable, collapsible bowl from diverted materials often led to an unattractive result.
Prototype 2: Buoy Bowl
At the Boulder Reservoir, we found abandoned LDPE buoys and docks and set out to turn them into dog bowls.
First, we pelletized both so they would melt evenly.
Then we used a George Foreman panini press to heat the LDPE plastic until it became plasticized enough to mold.
We used two generic dog bowls, wood, and clamps to shape the heated plastic into our first prototype bowl.
To make the bowl more appealing, we melted pieces of the tan dock with the buoy to create a marbled design.
Bowl 2
Bowl 3
Bowl 4
Prototype 3: Frisbee & Bucket Experiment
Next, we experimented with HDPE food buckets and frisbee discs donated by local companies.
Using the panini press, we melted the materials and shaped them into a bowl using an ABS-printed compression mold.
The ABS couldn't withstand the heat, but buckets and frisbees worked well as materials.
Final Prototype: Making the Mold
Each bowl started by melting 140g of colored frisbee and 460g of white bucket.
The plastic was twisted for a marbled effect, placed over the mold, and compressed with a 50-ton bottle jack.
After cooling, the bowl was trimmed and tagged.
The final mold was designed in Fusion360 and fabricated with a CNC mill to produce the MDF compression mold.
Baltic wood and guide pins were added to reinforce the mold.
Finally, three coats of epoxy were applied to secure the MDF fibers and enhance durability.